Production Process
Cutting
In our billet cutting process, the high-speed billet sawing-machine trims billet precisely in length andunits and prepare for the next process.
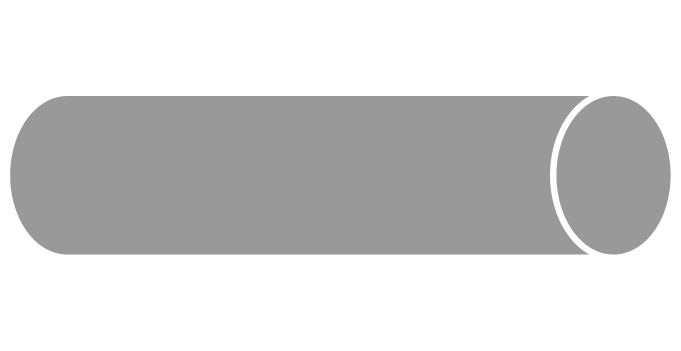
Extruding
Our extrusion process starts from preparing a billet by heating it at approximately 500 Celsius.
After this treatment, the billet is pushed through a die to create product in desired shapes. Extrusions are quenched by air or water depending on the desired alloys.Extrusions are also stretched to eliminate strains and cut into desired length.
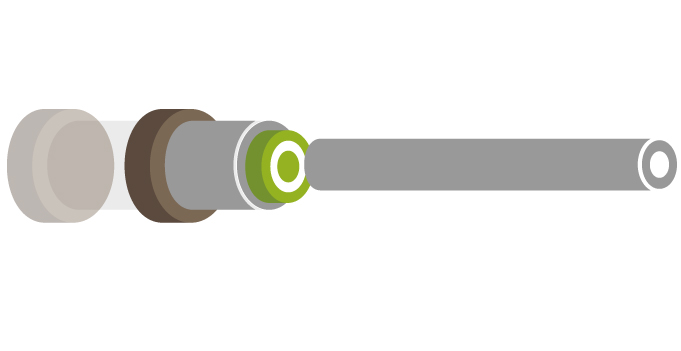
Heating
After the extrusion,the product get on tempering and annealed process in to order to accelerate Mechanical Property of Material before providing it to our customers.
At this process we also carried out the production of seamless pipes. A hollow pipe is usually processed and manufactured by die. To be able to answer wider customers need, we provide the double-action extrusion press, to produce a hollow pipe by functions of extrusion press.
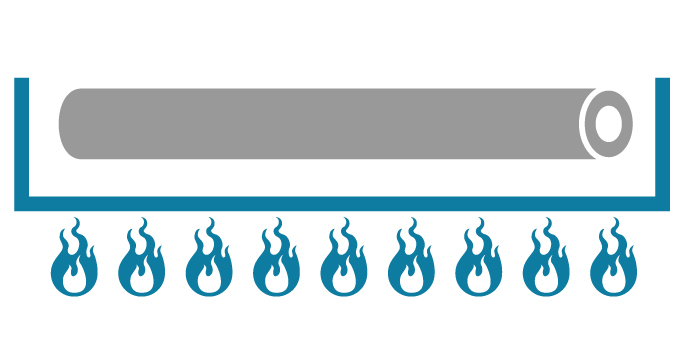
Drawing
The drawing process is a part of our integrated productions system.In keeping with the slogan, "Harder and more accurate tolerances,"we prepare for the cold processing equipment to set your request for the extruded pipes and bars.
The drawing process is the process which firstly we attach a tool called "plug" inside the pipe.Then, we clutch the head part of the pipe placed with a die and draw it out.
In case of drawing out in speed, we administer lubricating operation inside and outside the pipe.
Our maximum diameter for the drawing is 200mm.
After drawing, we are ready to process it to the tempering furnace to produce varieties of alloys.
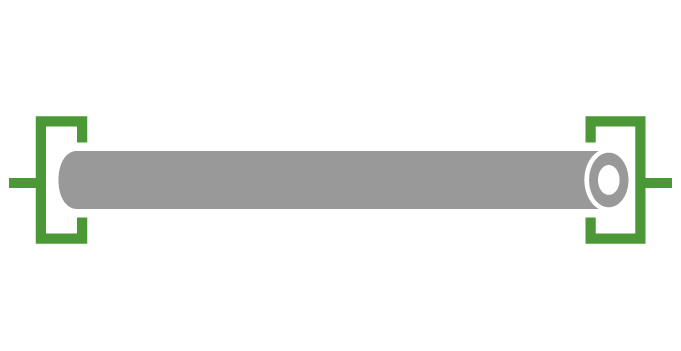
Processing
The extruded product is then precision cut, milled, and pressed to meet the demands of our customers.
We can provide a level of cutting tolerance not offered on most production lines. The variety of equipment we have on hand allows us to provide our customers with products that are very close to their desired end products.
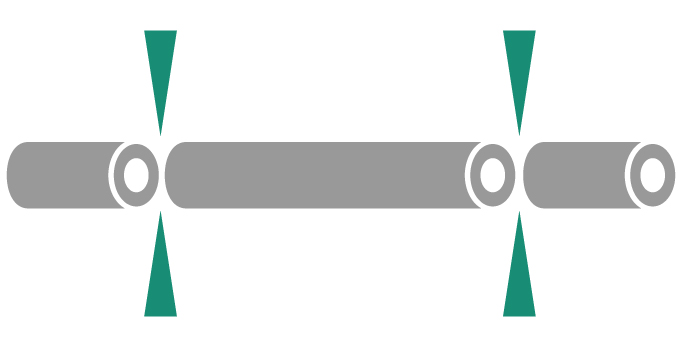
Inspection
Our Quality Control Section ensures the product meets customers' specification.Mechanical strength, chemical composition, measurements, and JIS are all tested and guaranteed.
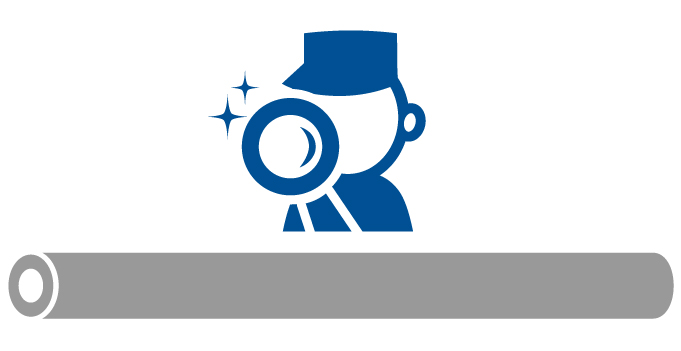
Shipping
After Quality Control Section performed their inspection process, products go to visual inspection and packing process. We inspect, and packed in packaging forms specified by customers, labeled online each item, and prepare for shipping to customers in time.
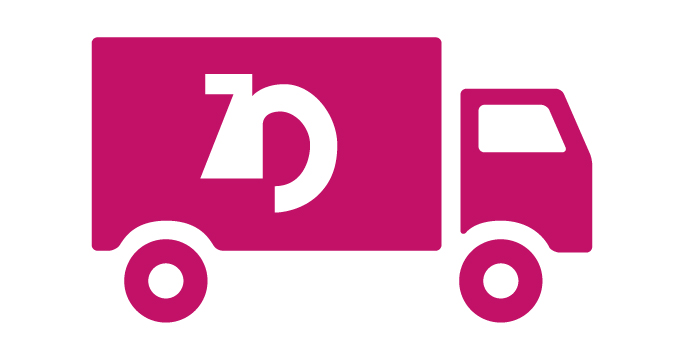
Die Making
Our Integrated Production depends on our die production.It is the core of all our manufacturing innovations and technologies.We prepare CAD connected NC Machines, EDM Machines, and Vacuum Hardening Furnace and more to satisfy customers in delivery time and dimensional accuracy of measurements.
Total of over 20,000 different die are produced here.Our craftsmanship will be handed down to the next generations.
Casting
Our manufacturing process starts from casting.
Aluminum is a great metal for recycling, so we recycle scraps generated in the manufacturing process
and also use ingot to produce a variety of aluminum alloys.Once Aluminum is melted in our melting furnace, we accommodate and assure ordered chemical composition of the melted Aluminum. Then we tap off it every single time.So that we are capable to meet customers' timeline and produce different alloys at every casting process.
Our aluminum alloys are produced by the continuous billet-casting furnace in length of 4.5 meters.All billets are tested by supersonic flaw detector, and are heat treated to make them homogeneous billets.